Cause and Effect Diagram
A cause and effect diagram, also known as an Ishikawa diagram, is a visual tool used to identify the potential causes of a problem or event. It is often used in quality control and process improvement. The diagram is shaped like a fishbone, with the problem or event at the head of the fish and the potential causes branching off from the backbone.
To create a cause and effect diagram, follow these steps:
- Identify the problem or event you want to analyze.
- Draw a horizontal line and write the problem or event at the right end.
- Draw a vertical line perpendicular to the horizontal line, extending from the left end of the horizontal line to the right end of the horizontal line.
- Draw four or more diagonal lines extending from the vertical line to the horizontal line, each representing a different category of potential causes.
- Brainstorm potential causes for the problem or event and write them on the diagonal lines.
- Review the diagram and identify any additional potential causes.
Cause and effect diagrams can be used to identify the root causes of a problem or event, which can help to develop effective solutions.
Benefits of using a cause and effect diagram:
- Helps to identify the root causes of a problem or event.
- Can help to develop effective solutions.
- Improves communication and collaboration between team members.
- Can be used to track progress and identify areas for improvement.
Tips for using a cause and effect diagram:
- Use a clear and concise problem or event statement.
- Brainstorm as many potential causes as possible.
- Group potential causes into categories.
- Use data to support your analysis.
- Review the diagram regularly and update it as needed.
Cause and effect diagrams are a valuable tool for identifying the root causes of problems and developing effective solutions. By following the steps and tips outlined above, you can create a cause and effect diagram that will help you to improve your quality and processes.
Key Aspects of Cause and Effect Diagrams
Cause and effect diagrams, also known as Ishikawa diagrams, are visual tools used to identify the potential causes of a problem or event. They are often used in quality control and process improvement.
- Visual: Cause and effect diagrams are visual representations of the relationship between a problem or event and its potential causes.
- Structured: The diagram is structured in a way that helps to organize and categorize potential causes.
- Logical: The diagram follows a logical progression from the problem or event to the potential causes.
- Comprehensive: The diagram can be used to identify a wide range of potential causes, including both direct and indirect causes.
- Collaborative: The diagram can be used by a team of people to brainstorm and identify potential causes.
- Actionable: The diagram can be used to develop action plans to address the potential causes of a problem or event.
- Preventive: The diagram can be used to identify potential causes of problems before they occur, which can help to prevent problems from happening in the first place.
Cause and effect diagrams are a valuable tool for identifying the root causes of problems and developing effective solutions. By understanding the key aspects of cause and effect diagrams, you can use them to improve your quality and processes.
Visual
The visual nature of cause and effect diagrams is one of their key strengths. By representing the relationship between a problem or event and its potential causes in a visual way, cause and effect diagrams make it easier to see the big picture and to identify the root causes of problems.
For example, a manufacturing company might use a cause and effect diagram to identify the potential causes of a defect in one of their products. By visually representing the relationship between the defect and its potential causes, the company can more easily see which factors are most likely to be contributing to the problem.
Cause and effect diagrams can also be used to identify the potential causes of problems before they occur. By visually representing the relationship between a potential problem and its potential causes, companies can take steps to prevent the problem from happening in the first place.
The visual nature of cause and effect diagrams makes them a valuable tool for identifying and solving problems. By representing the relationship between a problem or event and its potential causes in a visual way, cause and effect diagrams make it easier to see the big picture and to take steps to address the root causes of problems.
Structured
The structured nature of cause and effect diagrams is one of their key strengths. By organizing and categorizing potential causes, cause and effect diagrams make it easier to identify the root causes of problems.
-
Facet 1: Categories
Cause and effect diagrams typically use four main categories to organize potential causes: materials, methods, manpower, and machinery. This categorization helps to ensure that all potential causes are considered and that they are grouped in a logical way. -
Facet 2: Sub-categories
Within each main category, there may be several sub-categories. For example, the “materials” category might include sub-categories such as “raw materials,” “components,” and “packaging.” This further categorization helps to narrow down the potential causes and to identify the most likely root causes. -
Facet 3: Root causes
The root cause of a problem is the underlying cause that, if eliminated, would prevent the problem from recurring. Cause and effect diagrams can help to identify the root cause of a problem by tracing the potential causes back to their source. -
Facet 4: Action plan
Once the root cause of a problem has been identified, an action plan can be developed to address the root cause and prevent the problem from recurring. Cause and effect diagrams can be used to develop action plans by identifying the specific actions that need to be taken to address the root cause.
The structured nature of cause and effect diagrams makes them a valuable tool for identifying and solving problems. By organizing and categorizing potential causes, cause and effect diagrams make it easier to identify the root causes of problems and to develop effective action plans to address those root causes.
Logical
The logical nature of cause and effect diagrams is one of their key strengths. By following a logical progression from the problem or event to the potential causes, cause and effect diagrams make it easier to identify the root causes of problems.
The logical progression of a cause and effect diagram is typically as follows:
- The problem or event is identified.
- The potential causes of the problem or event are identified.
- The potential causes are organized and categorized.
- The root cause of the problem or event is identified.
- An action plan is developed to address the root cause.
This logical progression helps to ensure that all potential causes are considered and that the root cause of the problem or event is identified.
For example, a manufacturing company might use a cause and effect diagram to identify the potential causes of a defect in one of their products. The company would start by identifying the problem or event (the defect). Then, they would identify the potential causes of the defect. The potential causes would then be organized and categorized. The company would then identify the root cause of the defect. Finally, the company would develop an action plan to address the root cause.
The logical nature of cause and effect diagrams makes them a valuable tool for identifying and solving problems. By following a logical progression from the problem or event to the potential causes, cause and effect diagrams make it easier to identify the root causes of problems and to develop effective action plans to address those root causes.
Comprehensive
Cause and effect diagrams are comprehensive because they can be used to identify a wide range of potential causes, including both direct and indirect causes. This is important because it allows users to get a complete picture of the factors that may be contributing to a problem or event.
Direct causes are those that directly lead to a problem or event. For example, if a machine breaks down, the direct cause may be a faulty part. Indirect causes are those that do not directly lead to a problem or event, but which may create the conditions that allow the problem or event to occur. For example, if a machine is not properly maintained, this may create the conditions that allow a faulty part to cause the machine to break down.
By considering both direct and indirect causes, cause and effect diagrams can help users to identify the root causes of problems and develop effective solutions. For example, if a manufacturing company is experiencing a high rate of defects in one of their products, a cause and effect diagram could be used to identify the potential causes of the defects. The diagram could identify both direct causes, such as faulty parts or improper assembly, and indirect causes, such as lack of training or inadequate maintenance. By addressing both the direct and indirect causes, the company could develop a comprehensive solution to reduce the rate of defects.
Cause and effect diagrams are a valuable tool for identifying and solving problems. Their comprehensive nature allows users to consider a wide range of potential causes, including both direct and indirect causes. This helps to ensure that the root causes of problems are identified and that effective solutions are developed.
Collaborative
Cause and effect diagrams are collaborative tools that can be used by a team of people to brainstorm and identify potential causes of a problem or event. This is important because it allows users to get a variety of perspectives on the problem and to identify potential causes that they may not have considered on their own.
For example, a manufacturing company might use a cause and effect diagram to identify the potential causes of a defect in one of their products. The team would start by brainstorming a list of potential causes. Then, they would use the cause and effect diagram to organize and categorize the potential causes. This would help the team to see the big picture and to identify the root causes of the defect.
Cause and effect diagrams are also useful for identifying potential causes of problems before they occur. By brainstorming a list of potential causes, teams can identify potential problems and take steps to prevent them from happening in the first place.
The collaborative nature of cause and effect diagrams makes them a valuable tool for identifying and solving problems. By using a cause and effect diagram, teams can get a variety of perspectives on the problem and identify potential causes that they may not have considered on their own. This helps to ensure that the root causes of problems are identified and that effective solutions are developed.
Actionable
Cause and effect diagrams are actionable because they can be used to develop action plans to address the potential causes of a problem or event. This is important because it allows users to take concrete steps to solve problems and prevent them from recurring.
-
Identifying root causes
Cause and effect diagrams can be used to identify the root causes of problems. This is important because it allows users to develop targeted action plans that address the underlying causes of problems, rather than just the symptoms. -
Prioritizing actions
Cause and effect diagrams can be used to prioritize actions based on their potential impact. This is important because it allows users to focus their efforts on the actions that are most likely to solve the problem. -
Developing action plans
Cause and effect diagrams can be used to develop detailed action plans that specify the actions that need to be taken, who is responsible for taking the actions, and the timeline for completing the actions. -
Monitoring progress
Cause and effect diagrams can be used to monitor progress in addressing the potential causes of a problem or event. This is important because it allows users to track their progress and make adjustments to their action plans as needed.
The actionable nature of cause and effect diagrams makes them a valuable tool for solving problems and preventing them from recurring. By using a cause and effect diagram, users can identify the root causes of problems, prioritize actions, develop action plans, and monitor progress. This helps to ensure that problems are solved effectively and efficiently.
Preventive
Cause and effect diagrams are preventive because they can be used to identify potential causes of problems before they occur. This is important because it allows users to take steps to prevent problems from happening in the first place.
For example, a manufacturing company might use a cause and effect diagram to identify the potential causes of defects in one of their products. By identifying the potential causes of defects, the company can take steps to prevent the defects from occurring in the first place. This could involve making changes to the manufacturing process, improving quality control, or training employees on how to prevent defects.
Cause and effect diagrams can also be used to prevent problems from occurring in other areas of an organization. For example, a hospital might use a cause and effect diagram to identify the potential causes of patient falls. By identifying the potential causes of patient falls, the hospital can take steps to prevent the falls from occurring in the first place. This could involve making changes to the hospital environment, improving patient care, or educating patients on how to prevent falls.
The preventive nature of cause and effect diagrams makes them a valuable tool for preventing problems from occurring. By using a cause and effect diagram, organizations can identify potential causes of problems and take steps to prevent those problems from happening in the first place.
A cause and effect diagram, also known as a fishbone diagram or Ishikawa diagram, is a visual tool used to identify the potential causes of a problem or event. It is often used in quality control, process improvement, and problem-solving.
The cause and effect diagram was developed by Japanese quality control expert Kaoru Ishikawa in the 1960s. It is a simple but effective tool that can be used to identify a wide range of potential causes, including both direct and indirect causes.
The cause and effect diagram is a valuable tool for identifying and solving problems. It can be used to:
- Identify the root causes of problems
- Develop effective solutions
- Prevent problems from recurring
The cause and effect diagram is a versatile tool that can be used in a variety of settings. It is a valuable tool for anyone who wants to improve quality, solve problems, and prevent problems from recurring.
Cause and Effect Diagram FAQs
The cause and effect diagram, also known as the fishbone diagram or Ishikawa diagram, is a visual tool used to identify the potential causes of a problem or event. It is often used in quality control, process improvement, and problem-solving.
Question 1: What is a cause and effect diagram?
Answer: A cause and effect diagram is a visual tool used to identify the potential causes of a problem or event. It is often used in quality control, process improvement, and problem-solving.
Question 2: Who developed the cause and effect diagram?
Answer: The cause and effect diagram was developed by Japanese quality control expert Kaoru Ishikawa in the 1960s.
Question 3: What are the benefits of using a cause and effect diagram?
Answer: The cause and effect diagram can be used to identify the root causes of problems, develop effective solutions, and prevent problems from recurring.
Question 4: How do I create a cause and effect diagram?
Answer: To create a cause and effect diagram, follow these steps:
- Identify the problem or event you want to analyze.
- Draw a horizontal line and write the problem or event at the right end.
- Draw a vertical line perpendicular to the horizontal line, extending from the left end of the horizontal line to the right end of the horizontal line.
- Draw four or more diagonal lines extending from the vertical line to the horizontal line, each representing a different category of potential causes.
- Brainstorm potential causes for the problem or event and write them on the diagonal lines.
- Review the diagram and identify any additional potential causes.
Question 5: What are some tips for using a cause and effect diagram?
Answer: Here are some tips for using a cause and effect diagram:
- Use a clear and concise problem or event statement.
- Brainstorm as many potential causes as possible.
- Group potential causes into categories.
- Use data to support your analysis.
- Review the diagram regularly and update it as needed.
Question 6: What are some common misconceptions about cause and effect diagrams?
Answer: Some common misconceptions about cause and effect diagrams include:
- Cause and effect diagrams are only useful for identifying the root causes of problems.
- Cause and effect diagrams are difficult to create.
- Cause and effect diagrams are only useful for large and complex problems.
Summary of key takeaways or final thought:
The cause and effect diagram is a valuable tool for identifying and solving problems. It is a simple but effective tool that can be used to identify a wide range of potential causes, including both direct and indirect causes. By understanding the basics of cause and effect diagrams, you can use them to improve quality, solve problems, and prevent problems from recurring.
Transition to the next article section:
Click here to learn more about cause and effect diagrams.
Conclusion
The cause and effect diagram is a valuable tool for identifying and solving problems. It is a simple but effective tool that can be used to identify a wide range of potential causes, including both direct and indirect causes. By understanding the basics of cause and effect diagrams, you can use them to improve quality, solve problems, and prevent problems from recurring.
Cause and effect diagrams are used in a variety of settings, including manufacturing, healthcare, and business. They are a valuable tool for anyone who wants to improve quality, solve problems, and prevent problems from recurring.
Youtube Video:
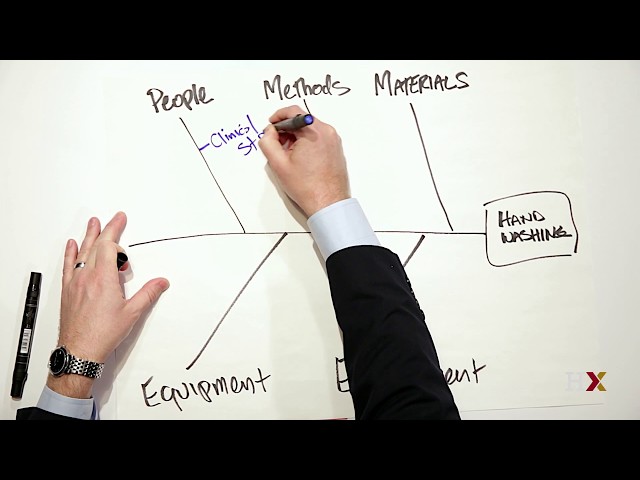