Ishikawa Cause-and-Effect Diagram
Ishikawa cause-and-effect diagrams, also known as fishbone diagrams due to their skeletal appearance, are visual tools used to identify and categorize potential causes of a problem or effect. Developed by Kaoru Ishikawa in the 1960s, these diagrams are widely employed in quality control and improvement processes.
To create an Ishikawa cause-and-effect diagram, follow these steps:
- Define the problem or effect: Clearly state the issue or outcome you wish to analyze.
- Draw the fishbone: Sketch a horizontal line representing the backbone of the fish. From the head of the fish, draw a vertical line downwards, representing the problem or effect.
- Identify main categories: Brainstorm and list the primary factors or categories that could contribute to the problem. These categories typically represent different aspects of a process or system, such as methods, materials, manpower, machinery, measurement, and environment.
- Draw branches: From the main categories, draw diagonal lines extending towards the backbone. These branches represent potential causes or contributing factors related to each category.
- Identify potential causes: Through brainstorming or data analysis, identify specific causes or factors that may have led to the problem. Write these causes along the branches.
- Analyze and prioritize: Examine the potential causes and determine their likelihood and impact. Prioritize the most significant causes for further investigation or action.
- Develop solutions: Based on the analysis, develop and implement solutions to address the identified causes and prevent the problem from recurring.
Benefits of Ishikawa Cause-and-Effect Diagrams
- Provide a structured and visual representation of potential causes.
- Foster collaboration and brainstorming among team members.
- Help identify root causes and prevent recurrence of problems.
- Improve process efficiency and quality.
- Facilitate data-driven decision making.
Tips for Effective Ishikawa Cause-and-Effect Diagrams
- Be specific: Clearly define the problem and identify specific potential causes.
- Use data: Support your analysis with data and evidence whenever possible.
- Encourage participation: Involve all relevant stakeholders in the brainstorming and analysis process.
- Prioritize effectively: Focus on the most significant causes and develop targeted solutions.
- Use technology: Leverage software or online tools to create and share Ishikawa diagrams.
- Review and update: Regularly review and update your Ishikawa diagrams to reflect changes and improve effectiveness.
Ishikawa cause-and-effect diagrams are powerful tools for problem-solving and process improvement. By following the steps and guidelines outlined above, you can effectively identify, analyze, and address the root causes of problems, leading to improved outcomes and enhanced quality.
Ishikawa Cause-and-Effect Diagram
Ishikawa cause-and-effect diagrams, also known as fishbone diagrams, are widely used in quality control and improvement processes. They help identify and categorize potential causes of a problem or effect. Here are eight key aspects to consider when using Ishikawa cause-and-effect diagrams:
- Visual representation: Ishikawa diagrams provide a visual representation of potential causes, making them easy to understand and analyze.
- Root cause identification: By identifying potential causes and their relationships, Ishikawa diagrams help uncover root causes of problems.
- Team collaboration: Ishikawa diagrams foster collaboration and brainstorming among team members, promoting diverse perspectives.
- Process improvement: By identifying and addressing root causes, Ishikawa diagrams contribute to process improvement and enhanced quality.
- Data-driven decision making: When supported by data, Ishikawa diagrams facilitate data-driven decision making and targeted problem-solving.
- Problem-solving tool: Ishikawa diagrams are a valuable tool for problem-solving, helping to identify and eliminate the root causes of problems.
- Quality control: Ishikawa diagrams play a crucial role in quality control by identifying and preventing potential problems.
- Continuous improvement: Ishikawa diagrams support continuous improvement efforts by providing a structured approach to problem analysis and solution development.
These key aspects highlight the versatility and effectiveness of Ishikawa cause-and-effect diagrams. They enable teams to visually represent and analyze potential causes, identify root causes, and develop targeted solutions, ultimately leading to process improvement and enhanced quality outcomes.
Visual representation
Ishikawa cause-and-effect diagrams, also known as fishbone diagrams, are widely recognized for their visual representation of potential causes. This visual aspect plays a significant role in enhancing understanding and analysis:
-
Schematic structure
Ishikawa diagrams employ a schematic structure resembling a fish skeleton. The main problem or effect is represented by the fish head, while the potential causes are categorized into different branches extending from the backbone. This structured layout provides a clear and organized visual representation of the cause-and-effect relationships. -
Graphical depiction
Unlike textual lists or tables, Ishikawa diagrams utilize graphical elements to depict potential causes. This visual representation allows users to quickly grasp the overall picture and identify patterns or relationships between different causes. -
Enhanced comprehension
The visual nature of Ishikawa diagrams makes them easier to understand than lengthy textual descriptions. By presenting information visually, users can more easily comprehend the connections between causes and effects, improving their ability to analyze and identify root causes. -
Improved communication
The visual representation of Ishikawa diagrams facilitates effective communication among team members and stakeholders. By sharing the diagram, teams can easily discuss and analyze potential causes, leading to better decision-making and problem-solving.
In summary, the visual representation of Ishikawa cause-and-effect diagrams is a key aspect that enhances understanding and analysis. By providing a structured, graphical depiction of potential causes, Ishikawa diagrams empower teams to effectively identify and address root causes, contributing to process improvement and enhanced outcomes.
Root cause identification
Ishikawa cause-and-effect diagrams, also known as fishbone diagrams, are renowned for their ability to identify root causes of problems. This capability stems from their systematic approach to categorizing and analyzing potential causes:
-
Comprehensive categorization
Ishikawa diagrams employ a comprehensive categorization system to group potential causes into relevant categories, such as materials, methods, manpower, machinery, measurement, and environment. This structured approach ensures that a wide range of potential causes is considered, increasing the likelihood of identifying the root cause. -
Cause-and-effect relationships
Ishikawa diagrams not only list potential causes but also explore their relationships. By visually depicting the cause-and-effect connections, the diagram helps users understand how different factors interact and contribute to the problem. This deeper understanding facilitates the identification of root causes. -
Logical analysis
The logical structure of Ishikawa diagrams promotes systematic analysis of potential causes. By tracing the branches of the diagram, users can logically eliminate less probable causes and focus on those that are more likely to be the root cause. This logical approach enhances the accuracy and efficiency of root cause identification. -
Team collaboration
Ishikawa diagrams encourage team collaboration in identifying root causes. By involving multiple perspectives and expertise, teams can brainstorm a wider range of potential causes and leverage diverse knowledge to pinpoint the most probable root cause.
In conclusion, the ability of Ishikawa cause-and-effect diagrams to identify root causes lies in their comprehensive categorization system, exploration of cause-and-effect relationships, logical analysis, and facilitation of team collaboration. By utilizing Ishikawa diagrams, teams can effectively uncover the underlying factors contributing to problems and develop targeted solutions for sustained improvement.
Team Collaboration
Ishikawa cause-and-effect diagrams, also known as fishbone diagrams, are renowned for their ability to foster collaboration and brainstorming among team members, promoting diverse perspectives. This collaborative aspect plays a crucial role in enhancing the effectiveness of Ishikawa diagrams:
-
Shared understanding
Ishikawa diagrams provide a shared visual representation of potential causes, ensuring that all team members have a common understanding of the problem and its potential contributing factors. This shared understanding facilitates effective brainstorming and discussion. -
Diverse perspectives
Team collaboration in Ishikawa diagram development encourages input from diverse perspectives and expertise. By involving multiple stakeholders, teams can consider a wider range of potential causes and identify those that may not have been apparent to a single individual. -
Synergistic problem-solving
The collaborative nature of Ishikawa diagrams promotes synergistic problem-solving. Team members can combine their knowledge and ideas to develop creative and effective solutions that address the root causes of the problem. -
Enhanced decision-making
By fostering collaboration and diverse perspectives, Ishikawa diagrams contribute to enhanced decision-making. Teams can make more informed decisions based on a comprehensive analysis of potential causes and their interrelationships.
In summary, the team collaboration aspect of Ishikawa cause-and-effect diagrams is a key factor in their effectiveness. By promoting shared understanding, diverse perspectives, synergistic problem-solving, and enhanced decision-making, Ishikawa diagrams empower teams to identify root causes and develop effective solutions.
Process Improvement
Ishikawa cause-and-effect diagrams, also known as fishbone diagrams, are renowned for their ability to contribute to process improvement and enhanced quality. This capability stems from their systematic approach to identifying and addressing root causes of problems:
-
Identification of Root Causes
Ishikawa diagrams help identify the root causes of problems by visually representing potential causes and their relationships. This comprehensive analysis enables teams to pinpoint the underlying factors contributing to the problem, rather than focusing on superficial symptoms. -
Targeted Problem-Solving
By identifying root causes, Ishikawa diagrams allow teams to develop targeted solutions that address the core issues. This targeted approach ensures that resources are allocated effectively and that solutions are likely to be successful in preventing the problem from recurring. -
Process Optimization
The identification and elimination of root causes through Ishikawa diagrams lead to process optimization. By addressing the underlying issues that contribute to problems, teams can improve the efficiency and effectiveness of their processes, resulting in enhanced quality and reduced waste. -
Continuous Improvement
Ishikawa diagrams support continuous improvement efforts by providing a structured approach to problem-solving. By regularly using Ishikawa diagrams to identify and address root causes, teams can create a culture of continuous improvement, leading to sustained quality enhancements.
In summary, the connection between process improvement and Ishikawa cause-and-effect diagrams lies in the ability of these diagrams to identify and address root causes. By providing a systematic approach to problem-solving, Ishikawa diagrams empower teams to optimize processes, enhance quality, and promote continuous improvement.
Data-driven decision making
Ishikawa cause-and-effect diagrams are powerful tools for data-driven decision making and targeted problem-solving. When supported by data, Ishikawa diagrams provide a structured framework to analyze potential causes and identify root causes of problems.
By incorporating data into Ishikawa diagrams, teams can:
- Quantify potential causes: Data can be used to assign weights or values to potential causes, enabling teams to prioritize and focus on the most significant factors.
- Identify patterns and trends: Data analysis can reveal patterns and trends in the occurrence of problems, helping teams identify underlying systemic issues.
- Validate solutions: Data can be used to test and validate potential solutions, ensuring that they are effective in addressing the root causes of problems.
For example, a manufacturing company experiencing high defect rates in a particular product line could use an Ishikawa diagram to identify potential causes. By collecting data on factors such as raw material quality, production processes, and equipment maintenance, the team could quantify the impact of each factor and prioritize their efforts to address the most significant causes.
Data-driven Ishikawa diagrams provide a structured and evidence-based approach to problem-solving, leading to more effective and targeted solutions. By leveraging data, teams can make informed decisions, allocate resources efficiently, and improve the overall quality of their processes.
Problem-solving tool
Ishikawa cause-and-effect diagrams, also known as fishbone diagrams, are renowned for their effectiveness as problem-solving tools. Their systematic approach to identifying and eliminating root causes empowers teams to address problems comprehensively and prevent their recurrence.
The connection between Ishikawa diagrams and problem-solving lies in their ability to:
- Visualize potential causes: Ishikawa diagrams provide a visual representation of potential causes, making it easier to identify and analyze their relationships.
- Identify root causes: By exploring the cause-and-effect relationships between potential causes, Ishikawa diagrams help teams pinpoint the underlying root causes of problems.
- Develop targeted solutions: Once root causes are identified, Ishikawa diagrams facilitate the development of targeted solutions that address the core issues and prevent problems from recurring.
For example, a manufacturing company experiencing high defect rates in a particular product line could use an Ishikawa diagram to identify potential causes. By categorizing potential causes into factors such as raw materials, production processes, and equipment maintenance, the team could visually analyze their relationships and identify the root causes contributing to the high defect rates. This understanding would then enable them to develop targeted solutions to address these root causes and improve product quality.
The practical significance of understanding the connection between Ishikawa diagrams and problem-solving lies in its ability to enhance problem-solving effectiveness. By using Ishikawa diagrams to identify root causes, teams can develop more effective and sustainable solutions, leading to improved process efficiency, reduced waste, and enhanced customer satisfaction.
Quality control
The connection between Ishikawa cause-and-effect diagrams and quality control lies in their ability to identify and prevent potential problems. Ishikawa diagrams provide a structured framework for analyzing potential causes of defects or quality issues, enabling teams to proactively address and eliminate them, thereby enhancing overall quality.
Ishikawa diagrams are particularly valuable in quality control for several reasons:
- Comprehensive analysis: Ishikawa diagrams consider a wide range of potential causes, ensuring that all factors contributing to a quality issue are identified and addressed.
- Root cause identification: By exploring the cause-and-effect relationships between potential causes, Ishikawa diagrams help teams pinpoint the underlying root causes of quality problems, enabling targeted and effective solutions.
- Preventive measures: Ishikawa diagrams facilitate the development of preventive measures by identifying potential causes before they lead to actual defects or quality issues. This proactive approach helps prevent problems from occurring in the first place.
For example, a manufacturing company experiencing high defect rates in a particular product line could use an Ishikawa diagram to identify potential causes. By categorizing potential causes into factors such as raw materials, production processes, and equipment maintenance, the team could analyze their relationships and identify the root causes contributing to the high defect rates. This understanding would then enable them to develop targeted solutions to address these root causes and prevent future defects, enhancing the overall quality of the product line.
The practical significance of understanding the connection between Ishikawa diagrams and quality control lies in the ability to improve product and process quality, reduce waste, and enhance customer satisfaction. By identifying and eliminating potential problems through Ishikawa diagrams, organizations can ensure the delivery of high-quality products and services, leading to increased customer loyalty and business success.
Continuous improvement
The connection between Ishikawa cause-and-effect diagrams and continuous improvement lies in their ability to provide a structured framework for identifying and addressing problems, leading to sustained improvements in processes and outcomes.
-
Root cause analysis
Ishikawa diagrams help teams identify the root causes of problems, rather than just treating symptoms. By understanding the underlying causes, teams can develop more effective solutions that prevent problems from recurring.
-
Process optimization
Ishikawa diagrams can be used to analyze and optimize processes, identifying areas for improvement and eliminating waste. By streamlining processes, teams can improve efficiency and effectiveness, leading to continuous improvement.
-
Data-driven decision-making
Ishikawa diagrams can incorporate data to support decision-making, ensuring that solutions are based on evidence and analysis. Data-driven decision-making leads to more effective problem-solving and continuous improvement.
-
Collaboration and knowledge sharing
Ishikawa diagrams foster collaboration among team members and stakeholders, promoting knowledge sharing and idea generation. This collaborative approach contributes to continuous improvement by leveraging diverse perspectives and expertise.
In summary, Ishikawa cause-and-effect diagrams play a crucial role in continuous improvement efforts by providing a structured framework for problem analysis, solution development, and data-driven decision-making. By understanding the connection between Ishikawa diagrams and continuous improvement, organizations can harness the power of this tool to drive sustained improvements in their processes and outcomes.
An Ishikawa cause-and-effect diagram, also known as a fishbone diagram, is a visual tool used to identify, categorize, and analyze potential causes of a problem or effect. Developed by Kaoru Ishikawa in the 1960s, it is widely employed in quality control and improvement processes.
The diagram resembles a fish skeleton, with the problem or effect represented by the fish head. The main categories of potential causes, such as materials, methods, manpower, machinery, measurement, and environment, are represented by the fish bones. Each category is further broken down into specific causes or factors that may contribute to the problem.
The Ishikawa cause-and-effect diagram is a valuable tool for several reasons. It provides a structured and systematic approach to problem-solving, helping teams to identify and analyze potential causes in a comprehensive manner. By visually representing the cause-and-effect relationships, it facilitates brainstorming, collaboration, and root cause identification. Additionally, the diagram promotes data-driven decision-making by incorporating quantitative data and evidence to support analysis and solution development.
Overall, the Ishikawa cause-and-effect diagram is a powerful tool for problem-solving and continuous improvement. It provides a structured framework for identifying, categorizing, and analyzing potential causes, leading to more effective and targeted solutions.
FAQs about Ishikawa Cause-and-Effect Diagrams
Ishikawa cause-and-effect diagrams, also known as fishbone diagrams, are widely used in quality control and improvement processes. Here are answers to some frequently asked questions about this valuable tool:
Question 1: What is an Ishikawa cause-and-effect diagram?
Answer: An Ishikawa cause-and-effect diagram is a visual tool used to identify, categorize, and analyze potential causes of a problem or effect. It resembles a fish skeleton, with the problem or effect represented by the fish head and the potential causes represented by the fish bones.
Question 2: How do I create an Ishikawa cause-and-effect diagram?
Answer: To create an Ishikawa diagram, start by clearly defining the problem or effect you wish to analyze. Then, identify the main categories of potential causes, such as materials, methods, manpower, machinery, measurement, and environment. Break down each category into specific causes or factors, and draw lines connecting them to the main categories and the fish head.
Question 3: What are the benefits of using an Ishikawa cause-and-effect diagram?
Answer: Ishikawa diagrams offer several benefits, including providing a structured approach to problem-solving, facilitating brainstorming and collaboration, identifying root causes, and promoting data-driven decision-making.
Question 4: When should I use an Ishikawa cause-and-effect diagram?
Answer: Ishikawa diagrams are particularly useful when trying to identify and analyze potential causes of a problem, especially when the problem is complex or has multiple potential causes.
Question 5: Are there any limitations to using an Ishikawa cause-and-effect diagram?
Answer: While Ishikawa diagrams are a valuable tool, they may not be suitable for all situations. For example, they may be less effective for problems with a large number of potential causes or for highly complex problems.
Question 6: Are there any alternatives to using an Ishikawa cause-and-effect diagram?
Answer: Yes, there are other problem-solving tools available, such as the 5 Whys analysis, fault tree analysis, and Pareto analysis. The choice of tool depends on the specific problem being analyzed and the preferences of the team.
In conclusion, Ishikawa cause-and-effect diagrams are a powerful tool for identifying, analyzing, and solving problems. By understanding their purpose, benefits, and limitations, you can effectively use Ishikawa diagrams to improve processes and outcomes.
Transition to the next article section:
Conclusion
The Ishikawa cause-and-effect diagram, also known as the fishbone diagram, is a valuable tool for identifying, categorizing, and analyzing potential causes of a problem or effect. It provides a structured and visual representation of the cause-and-effect relationships, facilitating brainstorming, collaboration, and root cause identification.
Ishikawa diagrams are widely used in quality control and improvement processes, but their applications extend to various fields, including manufacturing, healthcare, and business management. By understanding the purpose, benefits, and limitations of Ishikawa diagrams, individuals and teams can effectively utilize this tool to improve problem-solving, enhance decision-making, and drive continuous improvement.
Youtube Video:
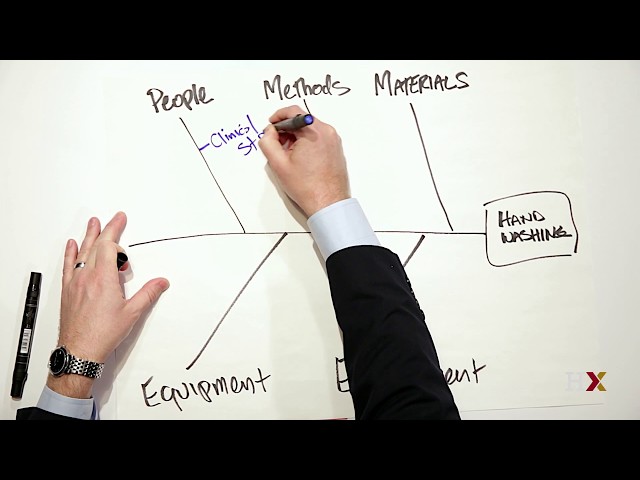